Carolina Handling National Forklift Safety Day
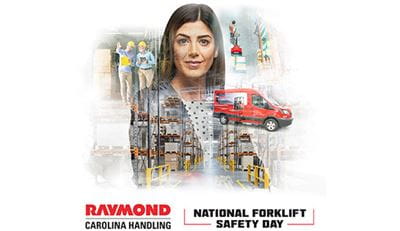
In recognition of National Forklift Safety Week, we asked CAROLINA HANDLING Safety Manager Mark Hernandez, a 23-year professional with considerable Environmental, Health and Safety experience, to talk about Safety.
In recognition of National Forklift Safety Week, we asked CAROLINA HANDLING Safety Manager Mark Hernandez, a 23-year professional with considerable Environmental, Health and Safety experience, to talk about Safety. In addition to what may have been expected, we learned about Pre-Op Inspections, how airplane and forklift training share some similarities, the importance of culture, that not all spotters work in NASCAR, and that pedestrians really do need training before walking into a warehouse.
Here is some of what we learned:
SAFETY STARTS AT THE TOP
Q. Where does safety start? How important is management support in having the safety commitment and safety initiatives, and how do you establish a safety-based culture?
Mark: All levels of leadership are critical where management sets the standards and implements programs to ensure they are communicated and understood by all Associates. Management must set the expectation of where safety should be. And then, through observations, not only the Associates and the operators observing, but also leadership, whether it is frontline or upper management.
When you observe deficiencies with work practices or processes, immediate action should be taken to correct them. And it does not always have to start with disciplinary action, but the expectations and the standards must be continuously reinforced to be effective. And that requires daily observations from not only the operators, pedestrians, frontline supervision, but also management.
In developing that culture, you must involve your Associates. It all starts with a written safety program and an operator training program for the forklifts or the industrial trucks. Once you have your programs in place, then you want to pull a group or team of your operators together and perform what I would call a learning team to get their input on the layout in regard to safe work practices.
START WITH THE BASICS
Q. What are the most basic and important things to help assure safety, especially as it relates to lift trucks?
Mark: We will start with the forklift operator. It is really important for a forklift operator to never operate a piece of equipment unless you're trained, certified and competent to operate it safely as well as always performing a daily pre-op check to ensure the equipment is safe to operate. In addition to that, the equipment should only be used as designed and within its load ratings.
And an operator should always remember that forklift operation is critical to their safety as well as the safety of the pedestrians. And that is life critical.
TRAINING
Q. How long does it take for someone to be trained on equipment? Are different people qualified or certified for different pieces of equipment or different uses?
Mark: Carolina Handling offers professional training courses for operators and pedestrians. We offer a training class, especially with a customer. The average time it takes is about six to eight hours to complete training for a new operator. We have technical and field trainers that offer that service to not only our customers, but also our Associates. The training we offer is called Safety On The Move. It is a Raymond product.
There is also a recertification process, required by the OSHA standard, which is 29 CFR 1910.178, and it requires that your operators be recertified every three years.
I mentioned earlier that a written safety program is important to have in place so that you set standards for your Associates. That program becomes the model that must be clearly communicated and understood by the operators at the time they receive their training and do their driving demonstrations to earn their certifications.
NEW MODELS
Q. Is training required for new models or new equipment?
Mark: Yes, that is required. Operators must be trained on the certain type and class of equipment, and if that changes, they have to go through an additional training course on that specific type and class to familiarize them with the operation and verify that they can safely operate it before you certify them on that type and class.
JUST LIKE AIRCRAFT
Q. That sounds like aircraft. You need to be certified as a pilot on different models, different equipment. The approach is that you do not just jump on a piece of equipment.
Mark: Exactly. And that's how OSHA wrote the standard. They want to make sure that if you are introducing a new class of equipment, you take the steps to train your operators on the operation and safe operation of that equipment and that you verify driving demonstrations so that they are competent enough to safely operate it before you certify them.
A SMART SYSTEM
Q. What tools does Carolina Handling offer that can help companies assure compliance?
Mark: We offer a product called iWAREHOUSE. For example, all the new reach trucks come outfitted with new hardware, digital display, and we offer customers the option to purchase our iWAREHOUSE system that has access control for operators. So, program administrators can restrict operation to only qualified operators through badges or employee numbers. It is a nice safety feature. It also walks the operator through the pre-op checklist, and it sends notification for impact events.
If an operator runs into a fixed object or racking system, it sends notification so that you know they were involved in a forklift incident. That is key. That is one product that we offer to improve safety that is really important to the industry.
The Safety On The Move training we offer to our Associates and customers, and then there's also a pedestrian safety course that's offered as well. And that one is called Steps To Safety. We do that because pedestrian safety is almost as important, if not more important, than the operator safety with Safety On The Move.
WALK SAFELY
Q. You mentioned pedestrian safety training. People may think, "Well, I know how to walk, why do I need to learn how to walk through a warehouse?”
Mark: There are a couple of examples of that. Because you have truck lanes and you have pedestrian lanes, OSHA expects that you designate those. Pedestrians need to stay in their lane, like a swim lane, and then the trucks stay in theirs.
Pedestrians have to be very careful because they are just like a normal intersection out on the roadway. When you come to intersections in a working environment, you have to make sure that you're looking both ways and you're making visual communication contact with the operators before you cross over their operating lanes or the lift trucks. You cannot just cut out in front of them or behind them without them seeing you. Many customers require pedestrians to wear Hi-Vis vests to increase visibility in operating areas. That can be life critical for a pedestrian. So, yes, it is very important in a manufacturing environment where you are operating a lot of forklifts.
The behavioral aspect becomes more important from a daily use. Daily safe operation becomes more important to the safety of the pedestrians and the operators. It is interesting. The operators always complain about the pedestrians and the pedestrians always complain about the operators and they have to work together, hand-in-hand and make sure that they maintain a safe work environment when they're coexisting safely in those work areas.
HIRING THE RIGHT PEOPLE
Q. What qualifications are companies typically looking for in hiring operators?
Mark: Different industries look for different things. Some companies have a lift truck operator as a more senior position. On the other hand, you see warehouse operations that have a large number of operators that come in at an entry level and are placed onto a forklift or a lift truck.
When you are selecting workers that have limited or no experience, that is when it is critical that you have an extensive training program and not just a training program to certify them, but also a mentoring program to improve their competencies. It would reinforce the safe operation until they gain the years of operating experience necessary to keep the risk down.
TURNOVER AND EXPERIENCE
Q. Is forklift operator turnover a problem or do operators tend to stay where they have been trained?
Mark: From the safety management side having experienced operators reduces your risk significantly, not only through the training and operating experience, but also the leadership within the company. Some companies reduce their risk by prohibiting temporary Associates from operating industrial trucks or forklifts because they are considered a high-risk operation, so, typically, in a work environment like that, where you have a lot of operating experience, your risk is much lower. You see a lot less incidents and less injuries. You do not typically see the serious injuries in that type of work environment.
Some environments have operators with lower levels of experience, fewer years of experience, and sometimes even temporary Associates operating forklifts for industrial trucks. You tend to see more incidents and injuries in those work environments, as well as serious injuries as a result of the inexperience with the operators.
REDUCING RISK
Q. How do companies address those safety concerns in a tight labor market?
Mark: That is when it becomes really important that companies reduce that risk by investing in effective training programs like Safety On The Move.
Customers that have work forces with less operating experience will often manage their risk by ordering trucks with additional safety features like iWarehouse to try to engineer out some of the risk to compensate for the lack of experience.
These trucks were designed to ANSI and OSHA standards as they come off the factory floor, and the customer then has the option to order additional safety features to reduce their risk, to try to engineer out some of that risk.
START YOUR WORK WITH A PROPER PRE-OP
Q. You mentioned the importance of a pre-op check of the equipment. What should operators be looking for in that pre-op? Is that every shift or every day?
Mark: Pre-operational or pre-op checks should be performed at the beginning of each shift if you are running on a shift schedule. On a single shift schedule, they should be performed at the beginning of the day or at least prior to the use of the equipment.
When you do a pre-op check, you turn the truck on, and it will do an operational self-check. Then you are going to verify things like your visual and audible alarms. All the trucks come standard with a visual alarm, like a flashing beacon. You are going to make sure that your brakes work, make sure your tires are in good condition, make sure your horn works, make sure you have a seatbelt, and that the seatbelt works. Some of the electric trucks come with an E-stop feature, which is a safety feature, you want to make sure that is functional and that the truck is operating correctly and there is no physical damage to it. No oil leaks or hydraulic leaks and just verify that the truck is safe prior to operating it. And always make sure the truck has fuel or a sufficient battery charge when beginning a shift.
THE OPERATING ENVIRONMENT
Q. How important is the environment that the equipment is being operated in? The layout, the design, the lighting, the traffic flows—do those all factor into safety?
Mark: Absolutely. The layout is very important when it comes to preventing accidents involving moving loads, racking systems, preventing collisions and, of course, pedestrian safety. I have experienced, personally, companies that have moved to LED lighting are not only benefiting from the energy efficiency, but also the increased visibility that is required for the safe operation of the forklifts. Of course, anytime an operator is stacking or racking materials, the loads must be properly secured to prevent accidents that can result in injury.
What is even more important is establishing that safety culture where you have operators or a team where everyone is engaged and having input on ways to improve the practices or operations with forklifts. They have opportunity to raise a concern if they see something that doesn't look right, or they see an accident waiting to happen. Employee engagement from that standpoint—to make continuous improvements as well as raise concerns—is an important part of the safety culture and effectiveness of your forklift safety program.
NASCAR ISNT THE ONLY PLACE FOR SPOTTERS
Q. How can other people help maintain a safe environment?
Mark: Other people in the warehouse can assist with safety by way of acting as what is called a spotter. So, for example, if you have an operator within an aisle it is either staging material or pulling material out of a racking system. In a retail environment like Home Depot or Lowe’s, you would have spotters stand by and make sure that customers do not get into those aisles where there is potential for material to fall.
In a warehouse operation, you have something similar where you use spotters when you are traveling in areas where you could have limited visibility or in areas where there are pedestrians nearby. You use a spotter to make sure that you have adequate clearance to travel.
Pedestrians also play a critical role in the safe operation of forklifts. Pedestrians should always be visible to the forklift operators and communicate with the forklift operators when they are in their work areas.
AVOIDING DISTRACTIONS
Q. Distracted driving is a growing issue on the road. Do forklift operators experience distractions?
Mark: When it comes to distractions, you see now is that a lot of companies are installing laptops or allowing cell phones and music speakers, on a lift truck. The laptop is required for operators to log transactions, so sometimes they can be a distraction. It must be clear that they are never to travel in that truck while distracted by that laptop or other devices like cell phones. That is something that we always stress with operators that have that type of equipment in front of them. The other thing is just distractions from people and pedestrians around them. Operators just must always maintain a high level of environmental and situational awareness.
NO SPEEDING
Q. Is speed a safety concern?
Mark: Depending on the spacing and the layout of the work environment or warehouse environment, speed can make a big difference in what is considered to be safe and at risk. So, you want your Associates to obviously have input on that. You want to make sure that your speed is set correctly to the spacing and the operation of the trucks as well as the operation around pedestrians.
What is common in a typical environment is somewhere in the range of five miles per hour when you are operating around pedestrians and racking systems. Where you are operating a truck that is traveling long distances across a distribution center, that might be set up as high as six to eight miles per hour. Speed does make a difference in the safety of the work environment; it has to be set to the layout and operations.
PRESSURE
Q. Is there sometimes pressure on operators, from a productivity standpoint, to push through certain volumes or numbers?
Mark: There can be. I am sure that, in certain work environments, there is a high demand for meeting a schedule. If you are in that type of work environment, you're always trying to keep up with the demands, rushing or operating in a hurry can increase risk of mistakes or accidents… If you had a work environment that was solely focused on output and productivity, and safety was just supposed to be a given, you're going to see a much higher at-risk working environment. Especially if people are trying to keep up with what the schedule demands, that does impact the “at risk” operating practices of operating forklift trucks.
This interview transcript has been lightly edited for length and clarity.