Training to achieve a culture of safety at your plant
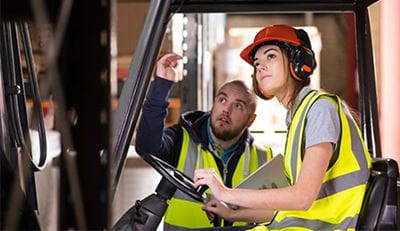
Creating a culture of safety is an ongoing process—it takes commitment to continuous improvement, and a willingness to train, retrain, and supervise forklift operators and pedestrians alike. Inspiring all employees to be accountable in supporting and sustaining a “‘training-first”’ mindset is imperative for achieving a productive work environment.
Previously published by PlantServices.com
Creating a culture of safety is an ongoing process—it takes commitment to continuous improvement, and a willingness to train, retrain, and supervise forklift operators and pedestrians alike. Inspiring all employees to be accountable in supporting and sustaining a “‘training-first”’ mindset is imperative for achieving a productive work environment.
To learn more about how Raymond supports the Industrial Truck Associations’ National Forklift Safety Day’s mission year- round, members of Raymond’s Solutions and Support Centers across the U.S. answered some of the industry’s most frequently asked questions regarding safety.
Q: What are your top tips to operate efficiently?
A: “Forklifts are an essential piece of equipment in many workplaces, especially in warehousing and manufacturing,” says Tom Hughes, corporate safety and training manager at Raymond Storage Concepts. “These vehicles make work more efficient. It is incumbent upon employers, however, to ensure operators of and pedestrians near forklifts are trained and supervised. Once trained, operators and pedestrians need to make sure they are practicing the skills that they learned 100%.”
Q: What is a key ingredient to help drive and sustain a healthy safety culture in your workplace?
A: Participation and engagement. All levels within your organization should support the cause, says Caleb Teltoe, quality assurance supervisor at Associated. “Everyone actively participating with one voice speaking a consistent message. Without the right people in the right places the program will never thrive. Everyone has a role when it comes to creating a successful workplace!”
Achieving a culture of safety takes more than just learning about safety, we must empower our people to take action when it is needed, says Teltoe. “When all employees feel they are contributing in caring for each other, and they see the leaders being committed to creating a healthy work environment, a culture of safety emerges.”
Q: In addition to eLearning, what are some other tools that Raymond offers to help train operators?
A: “Raymond’s iWAREHOUSE telematics system allows operations to effectively monitor labor resources and supervise employees,” says Mark Hernandez, safety manager at Carolina Handling. “For example, all the new reach trucks come outfitted with new hardware, digital display, and we offer customers the option to purchase our iWAREHOUSE system that has access control for operators.” Program administrators can restrict operation to only qualified operators through badges or employee numbers. It also walks the operator through the pre-op checklist.
“At Raymond, we believe that proper operator training and supervision can increase efficiency and create a productive workplace where all employees feel empowered to succeed,” says Hernandez. “Raymond offers industry-leading solutions to help educate forklift operators, lift truck technicians and pedestrians on best practices in material handling environments. A variety of learning tools and experiences are offered, including e-learning, classroom learning and virtual reality learning.”
For more information on how Raymond supports National Forklift Safety Day initiatives, visit https://www.raymondcorp.com/campaign/forkliftsafety.
This interview transcript has been lightly edited for length and clarity.